3D Printer: Prusa Clone
RepRap projects focus on open-source 3D printers, there are multiple type of materializing methods and multiple stage types.
I decided to make a Fused Deposition Modeling (FDM) printer with a Cartesian XYZ linear stage. We use a Mechatronic system that deposit hot plastic on a certain location, you could do manually by using a hot-glue gun.
Mechanics
So from that point I used the open-source CAD files to mill the Frame and Y-stage on the CNC mill at the D:DREAM Hall. A machine that I fixed a year earlier. The hardware I bought at GAMMA and the electronics I ordered at eBay.
The Orange parts were ordered online, they are made out of Poly Lactose Acid (PLA). It’s made out of corn and is fully bio degradable, so in the last years it needed some superglue to keep on working.
This resulted in the following printer:
Electronics
The electronics consists out of 5x Nema 17 stepper motors controlled by an Arduino Mega controller with a RAMPS-1.4 holding 4x DRV8825 Drivers.
- 1 Stepper motor for the X-stage
- 1 Stepper motor for the Y-stage
- 2 Stepper motors for the Z-stage
- 1 Stepper motor for the material extruder
Next to the motion control, two temperatures are also controlled by the Arduino Mega.
- Extruder, the alumium block that heats up the material using a simple heat element. The temperature is measured using NTC sensor and using a PID contoller is controlled.
- Heatbed, it’s a PCB that is controlled by a MOSFET. Using a PID controller, the needed temperature is maintained.
Informatica
After a 3D Model is drawn using a Computer Aided Design (CAD) like Solidworks. The movement paths need to be generated and send to the Arduino controller.
For 3D printer multiple Computer Aided Machining (CAM) software packages are available. I used Repetier-Host, since it came with an easy to setup firmware for the Arduino controller.
Update: In Jan 2019 I started the build of my second gen Prusa i3 Clone Printer. To do so, I partly upgrade the 3D Printer with autobed leveling, Bigtree Controller instead of the Arduino Mega with RAMPS, more quite TMC2130 stepper drivers, new direct drive extruder and new heatbed. So almost everything was temporary upgraded.
When the 2.0 is up and running, the 1.0 will be improved with a complete new extruder head and stiffened z-stage.
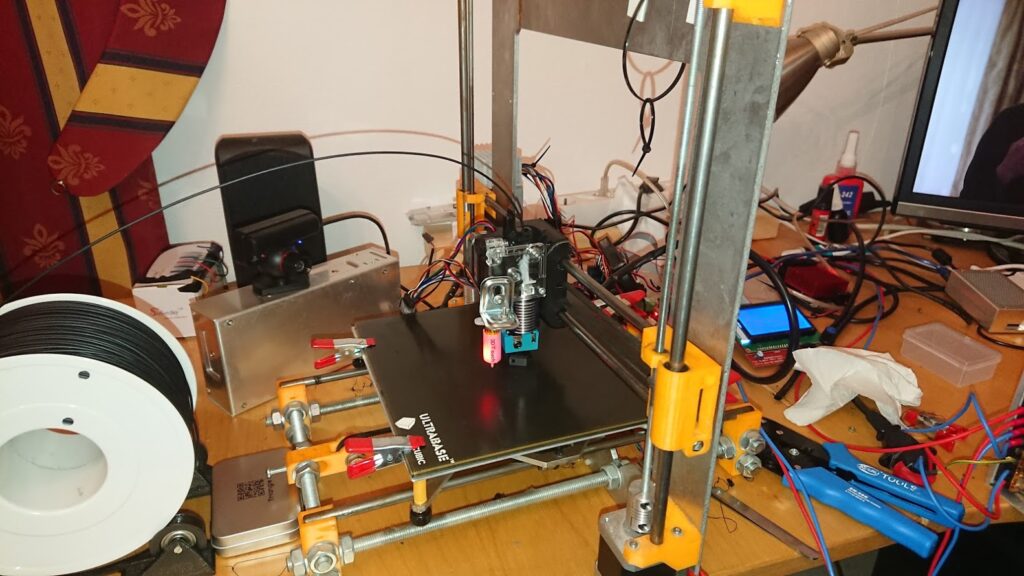
For people who are new to the multi-disciplinary term, mechatronica.
Mechatronica
– Mech from Mechanical
– Tron from Electronica
– Ica from Informatica